記事見出し
Koubaien, the master of Nara ink, delves into the essence of ink-making.
The name “sumi” is said to have originated from the word “stain” and has been passed down through the ages. Ink is a wonderful writing tool that lasts for years without fading or being eaten by insects.
Nara ink, dating back to the first year of Daitoku (806 AD), began when Kukai brought back ink-making techniques from Tang China along with brushes. He collected soot accumulated on the ceiling of the Mibutsudo Hall at Kofukuji Temple, mixed it with animal glue, and thus began the production. Even today, Nara ink accounts for over 90% of the national production.
全国で古梅園だけの墨造り製法
Koubaien, the only ink manufacturer in the country with its own ink-making method, has proudly flown its signboard since the Azuchi-Momoyama period, continuing to uphold traditional techniques in Nara City.
Koubaien is the only establishment in the country that manufactures ink from “collecting soot.” It is truly a one-of-a-kind presence.
The ink-making process, starting from “collecting soot,” involves lighting pure vegetable oil soaked in rushes on a wick, covering it with earthenware, and collecting the soot smoke that adheres to the earthenware.
To ensure that the soot adheres evenly, all 200 earthenware vessels are rotated every 20 minutes, and the soot collected on the underside of the lid is gathered with chicken feathers…
Oil-smoke ink extracted from two hundred flames
Even after tirelessly repeating the exhausting task for 8 hours, the amount collected does not exceed 1 kg. The outer walls of the smoke-extracting chamber are stained pitch black from the soot particles, turning the white walls completely black. Entering inside, one is enveloped in the heat from countless flames, leaving a fantastical and sacred impression.
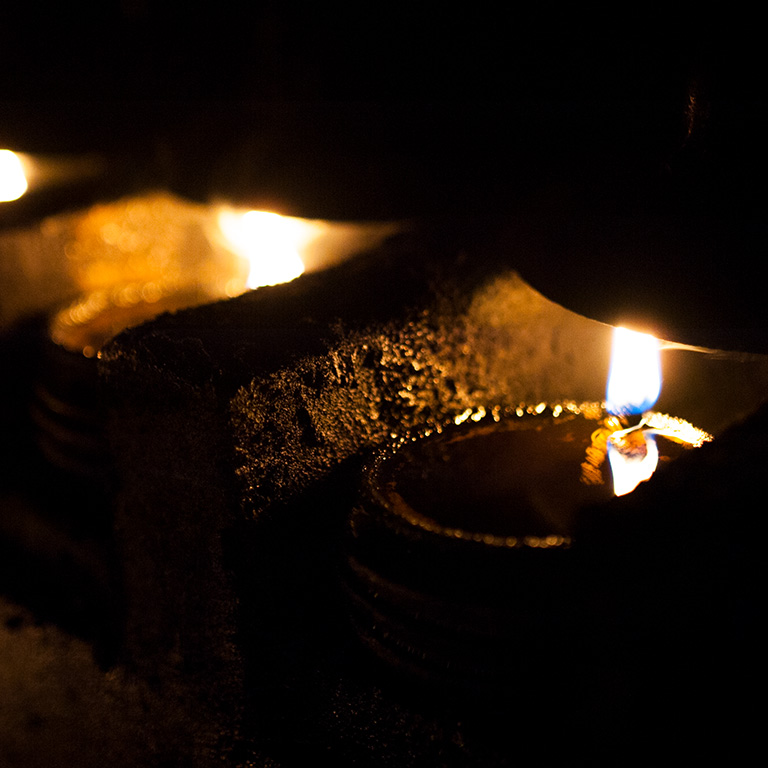
Premium quality glue with transparency
Ink is made by adding soot, glue, and fragrances. Glue, derived from animal bones or skins such as those of cows, is placed in double boilers, where it undergoes a long process of water bath heating to create a solution. Ink-making can only be done during the period of low temperatures from autumn to spring, to prevent the glue from spoiling. Anticipating a pungent smell… yet surprisingly, the smell is minimal, refined, with very few impurities, showcasing the unique transparency and elasticity of high-quality glue.
Employees unanimously affirm, “We use premium quality glue.” Witnessing the addition of soothing fragrances such as plum to the prepared soot and glue, the stage is set for the “ink master” to make their appearance. Finally, the crucial “mixing” process begins, determining the fate of the ink.
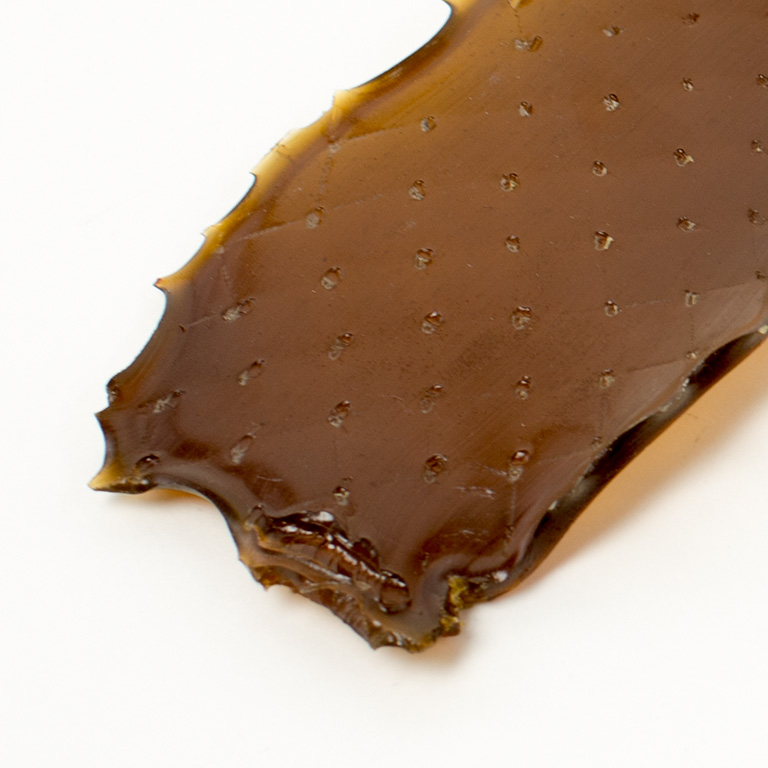
Ink mixing with skilled technique
The mochi-like raw ink is evenly kneaded with the feet until the ink balls shine, and then further refined by hand.
The “mixing” process significantly influences the quality of the ink.
Just before being placed into molds, the ink balls are shaped into cylindrical forms by the ink master’s hands. If the rolling during mixing deviates even slightly, it can cause warping or cracking in the ink after drying.
It’s surprising that the moment to stop mixing is indicated by the ink balls themselves. The finely tuned senses unique to skilled artisans enable them to discern the perfect moment without error.
Skilled technique of “molding” with controlled moisture level
The unit of weight for ink is called “cho.” (1 cho = 15g)
Taking into account the drying of moisture, approximately 22.5g of ink is put into the molds for 1 cho.
The slight difference is determined by the intuition of craftsmen who have calculated the temperature and humidity. The ink master’s intuition never fails.
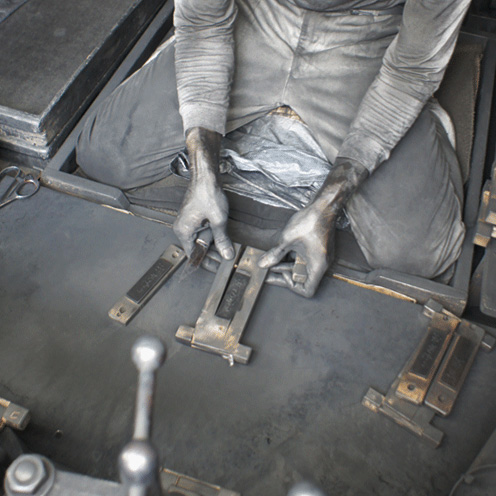
Careful drying using ash
The freshly molded ink, after completion of molding, is placed into wooden molds made of pear wood and secured with clamps.
The ink taken out from the wooden molds is soft, resembling “yokan” (a type of Japanese sweet bean jelly).
This ink undergoes “ash drying,” where the ash drying artisans come into play.
The ink taken out from the wooden molds is slowly dried while buried in the ash surrounding the ash drying room, arranged around wooden boxes.
Drying process with attention to moisture level
On the first day of drying, the ink is buried in ash with higher moisture content, and from the second day onwards, it is gradually transferred to ash with lower moisture content.
This ash drying process continues for about one week for small-sized ink and 30 to 40 days for large-sized ink.
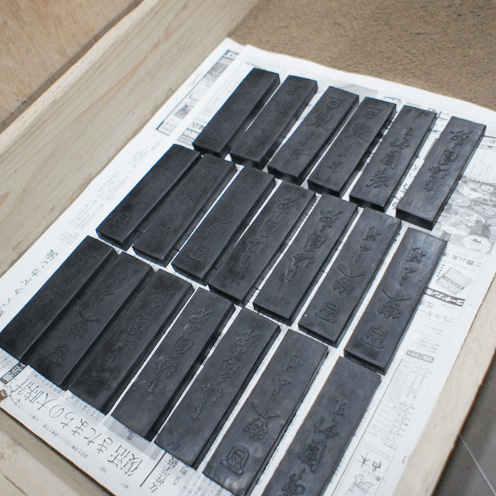
Completion of the Supreme Ink by the Master Ink Maker
After the ash drying process, the ink, with about 70% of its moisture removed, is further processed by weaving it with straw and hanging it from the ceiling indoors for natural drying. The drying period typically takes about two weeks to three months. Once the natural drying is completed, each ink piece is meticulously washed with water to remove any ash or other impurities adhering to the surface. Then, a secret finishing agent is applied to the surface for cosmetic purposes.
Some products undergo an additional process where the ink’s surface is roasted over charcoal to soften it and polished with clam shells until it shines. Every step of the process involves painstaking work.
Koubaien’s Ink Supported by Many Writers
The completed ink, after going through these processes, becomes a high-priced item when displayed in stores. However, the ink crafted through such intricate processes never fails to meet the expectations of artists. Products made with pride begin with the preparation of water for polishing the ink, paying attention to temperature and humidity, how to grind the ink, how to match the inkstone, selecting the paper…
Amidst the increasing popularity of “ink solutions,” there is still a strong trust from artists who have an unwavering love for genuine ink, believing that their artwork must be created with ink. Koubaien, persistently adhering to the techniques and methods developed over many years, embodies the essence of “PRIDE” through its unwavering commitment to meticulous craftsmanship.
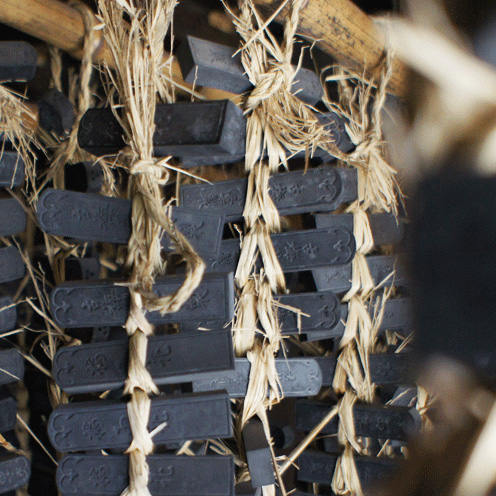
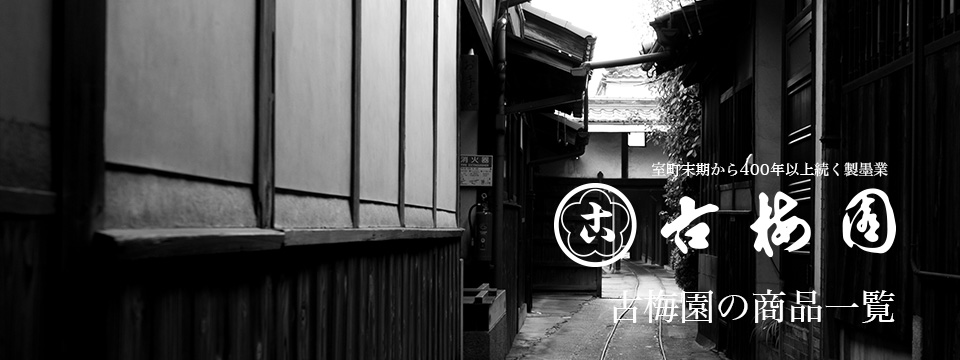